Sugar Rush Xmas(シュガーラッシュクリスマス)|Pragmatic ...
<ウェブサイト名>
<現在の時刻>
{{menuText}} Search Japanese Chinese Contact Us Quote About DAIDO STEEL Products R&D Investor Relations Sustainability Sustainability --> 学生の皆さまへ --> Initiatives to Counter Climate Change TOP Sustainability Environmental Initiatives to Counter Climate Change Font Size Normal Large Daido Steel’s businesses consume large amounts of energy. Daido Steel understands its responsibilities as a company that uses large amounts of energy, and prioritizes efforts to reduce CO2 emissions linked to energy use, which account for 85% of greenhouse gas emissions in Japan. The Japanese government’s Fifth Basic Energy Plan, which was approved by Cabinet decision in July 2018, calls upon companies to take on the challenges of energy transition and decarbonization towards 2050, and make every effort to realize its targeted energy mix by 2030. Daido Steel is ready to fulfill its responsibilities as a member of Japan’s steel industry by improving equipment and operations, as well as advancing the development of technologies, based on the Japan Iron and Steel Federation’s Commitment to a Low-Carbon Society. Heavy Investment in Energy Saving Measures Over the span of 24 years, from fiscal 1996 to fiscal 2019, Daido Steel has invested a total of ¥52.9 billion in energy-saving measures. In fiscal 2011, the Company has invested ¥19.8 billion in a 150-ton electric furnace with excellent energy efficiency. In fiscal 2016, the Company invested ¥4 billion to streamline its No. 2 continuous casting line in order to rectify molten steel distribution and increase the ratio of continuous casting for specialty stainless steel. For facilities that consume large amounts of fuel, such as heating furnaces, Daido Steel has expanded the application of regenerative burners that have better energy efficiency (burners that recover heat from effluent gas combustion) and oxygen combustion technologies. The Company is helping to reduce CO2 emissions while aiming to achieve its energy conservation targets, described later, by concentrating investments in energy-saving measures that include consistent yield improvements with an eye on 2030. Initiatives to Reduce EnergyLinked CO2 Emissions and Emissions per Ton of Production Daido Steel has successfully reduced CO2 emissions and emissions per ton of production through threepronged initiatives entailing (1) energy conservation, (2) fuel conversion, and (3) consistent yield improvements. On the energy conservation front, the Company has developed and constructed electric furnaces that excel in energy efficiency, switched to oxygen combustion for ladle preheating equipment in the steelmaking process, and expanded waste heat collection on heating furnaces. For fuel conversion, the Company has switched fuels to city gas, which has a low amount of CO2 emissions among fossil fuels. The Company has also improved yields by increasing the ratio of continuous casting. Reduction in Transportation CO2 Emissions Reducing CO2 emissions in transportation is an important avenue for combatting global warming. The heavy industry must transport heavy objects, and Daido Steel has coordinated with its supply chain to advance a modal shift* and improve facilities that support a modal shift. Additionally, we are focusing efforts on contributing to the environment by increasing distribution efficiency in a bid to cut CO2 emissions. Modal Shift On the transportation front, Daido Steel has consistently lowered its CO2 emissions per ton of steel as a result of modal shifts since fiscal 2003. To promote modal shifts, the Company has made investments in relevant areas. By constructing all-weather berths for ships carrying its steel materials, allowing shipments even in rainy weather, the Company has cut CO2 emissions per ton by roughly 20% for its steel products by relying on coastal vessels for transportation in a highly efficient environmental way. Daido Steel has also fabricated special uncovered containers that enhance transportation quality and loading efficiency. In 2003, the transportation of steel materials from its factories in the Nagoya region to the Niigata region was switched entirely from trucks to railways. In 2006, the same was done for steel transported from these factories to customers in the Akita and Niigata regions (fiscal 2019 results: 240,000 tons of steel wire, 10,000 tons of rebar annually). Furthermore, ferries are used for transportation to the Sendai region. In 2008, Daido Steel’s system for advancing modal shifts was recognized with the first Eco Ship Mark Certification. Daido Steel intends to further advance the modal shift from trucks to ships and railways. * Modal shift: Transportation that uses railways and ships instead of automobiles and airplanes. This can reduce CO2 emissions and conserve energy. Further Advancing Initiatives to Conserve Energy As a medium- to long-term objective for conserving energy, Daido Steel has set the target of reducing energy use by at least 10% by fiscal 2030 (fiscal 2013 BAU comparison). To achieve this objective, the Company has drawn up a road map and is making steady progress. [Pursuit of Energy Efficiency] To achieve this objective, Daido Steel is striving to thoroughly reduce heat loss by developing and introducing cutting-edge melting and heating technologies. We introduce our main initiatives below. Technology for Uniformly Melting Scrap Steel At the Chita Plant, the 150-ton electric furnace that began operating in November 2013 features the full application of technology for uniformly melting scrap steel with a furnace rotating mechanism developed in-house. Along with rectifying molten steel distribution, the Company has improved energy efficiency per ton of production by 15% for the entire process, from melting to casting, compared with the previous 80-ton electric furnace. By rotating the furnace, cold spots move closer to the electrodes for a more uniform melting process that boosts energy efficiency Technology for Oxygen Combustion Oxygen combustion results in high flame temperatures and lower emissions of gases, so it can improve energy efficiency in temperature ranges above 1,000°C, which is often the case at Daido Steel. Taking as an example the ladle preheating equipment used in the steelmaking process (right diagram), the Company has reduced energy use by 40% compared with previous air combustion methods. Daido Steel is expanding the application of oxygen combustion to soaking furnaces and continuous casting tundish preheating equipment. Reducing Thermal Capacity of Heating Furnace Refractory Materials Daido Steel has more than 150 heating furnaces and heat treatment furnaces. Reducing the weight of refractory materials is an effective way to reduce energy usage when temperatures rise quickly from room temperature to furnace temperatures. By deploying ceramic fiber, which is as light as possible and has excellent insulation properties, in forging heating furnaces, Daido Steel has cut energy usage by 13% (see photo on right). Sustainability Environmental Policy Management Load Reduction Activities Against Global Warming Reductions in Emissions Recycling-based Society TOP Sustainability Environmental Initiatives to Counter Climate Change About DAIDO STEEL Products R&D Investor Relations Sustainability Sustainability --> Students --> Contact Us Quote Site Map Privacy Policy 電子公告 --> Terms of Use Japanese Chinese Copyright©1996-2024 Daido Steel Co., Ltd. search CLOSE
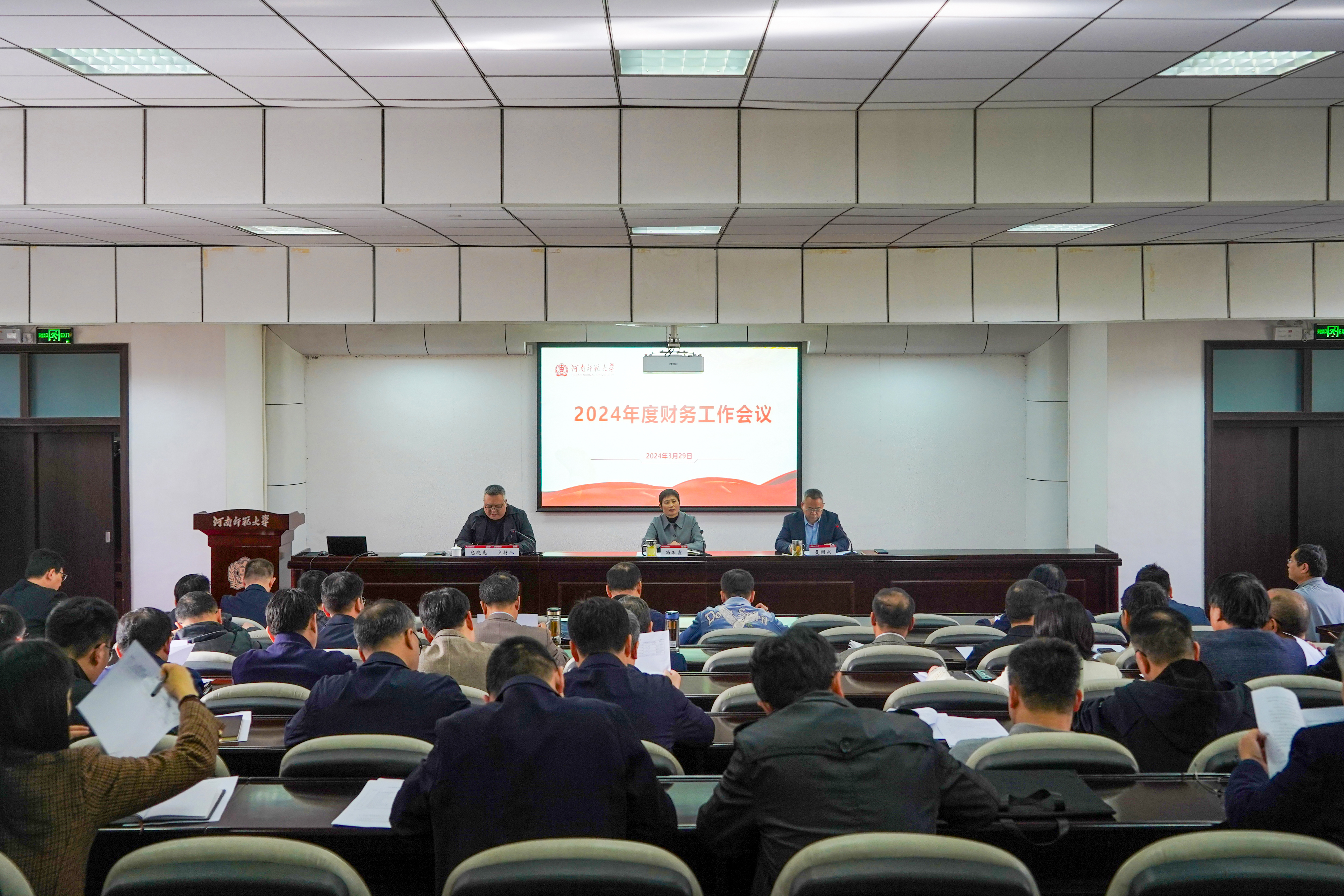